The joint in abrasive belts
The joint is the most vulnerable part of an abrasive belt during the sanding process. Knowing the types of joints available, their characteristics and which joint is appropriate each sanding application is key to avoiding problems like:
Parallel marks caused by the belt joint.
Belt vibrations.
Accumulations of residue on the joint.
Wrong direction of rotation of the abrasive belt
Belt breakage.
At Abracom, as a specialist manufacturer of abrasive belts, we make all types of joint necessary for each type of industry and its different sanding applications.
To be taken into account
Overlapped joint
We use this joint for sanding belts with FABRIC or PAPER backings to obtain the best finishes. The joint has the same thickness as the rest of the abrasive belt. It requires taking into account the direction of rotation of the belt.
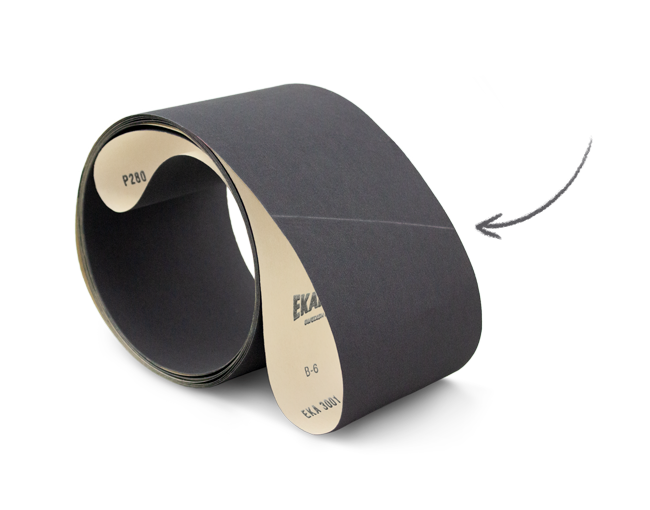
Recessed Overlapped joint
We manufacture this joint for abrasive belts with FLEXIBLE FABRIC backing. This type of joint is suitable on fine grits for edge sanding, soft surface sanding and where vibration risks may exist. This joint has a recess, grit interruption, by way of compensation on the abrasive side, we make the joint 7mm wide. It requires taking into account the direction of rotation of the belt.
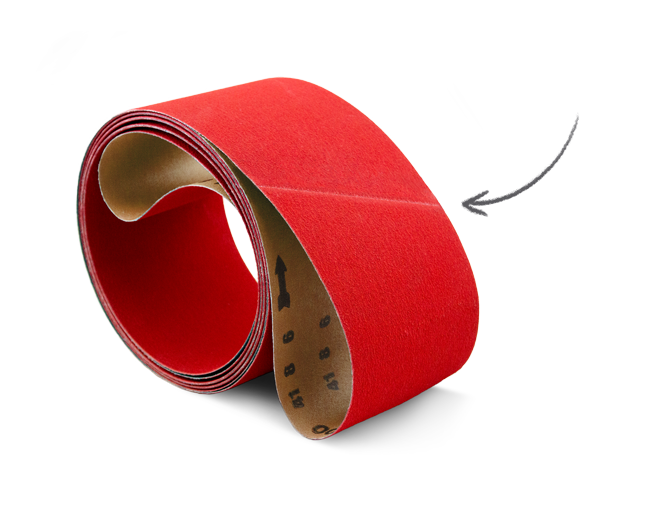
End joint
We manufacture this joint in abrasive belts with FABRIC, FILM and NON-WOVEN FABRIC supports. The end result is a joint with a tolerance very close to zero with respect to the belt thickness. It is bidirectional, it does not require taking into account the direction of rotation of the belt.
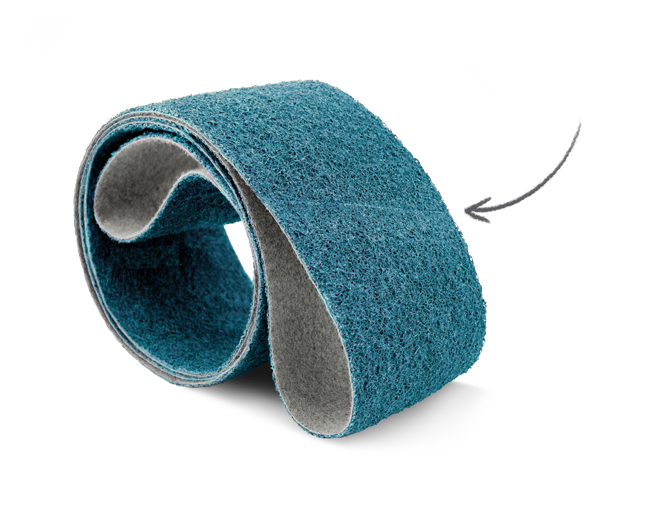
Special film tapes for end joints
Green Tape:
High-strength reinforced polyester film for demanding applications.
Thickness of 215 microns.
Grit range: 24,36,40.
Blue Tape:
High strength polyester film for heavy sanding.
Thickness of 165 microns.
Grit range: 60,80.
White Tape:
Polyester film combining high strength and excellent flexibility.
Thickness of 112 microns.
Grit range: 100,120,150.
Red Ribbon:
Thin polyester film for smooth sanding and increased flexibility.
Thickness of 75 microns.
Grit range: 180, 220, 240, 280, 320, 400, 600.
Gold Ribbon:
Ultra-thin polyester film for a fine and smooth finish.
Thickness of 50 microns.
Grit range: 800, 1000
