Technologie du grain
Savoir quel minéral abrasif utiliser lors du ponçage est important non seulement pour éviter d’endommager les surfaces, mais aussi pour rendre l’opération de ponçage plus efficace et moins chronophage, ce qui est très apprécié car le ponçage est généralement une tâche monotone qui prend du temps et qui est source d’inconfort pour les mains de l’opérateur.
Tous les matériaux n’ont pas la même dureté et se comportent donc différemment lorsqu’ils sont traités mécaniquement. Malheureusement, ce point est souvent négligé entraînant une perte de temps et de ressources et, en fin de compte, une augmentation du coût du ponçage.
Les minéraux utilisés aujourd’hui sont tous d’origine synthétique, car ils offrent de plus grands avantages et une plus grande uniformité dans toutes leurs propriétés, ce qui est décisif lors des applications industrielles.
Forme et structure des minéraux
Connaître leur forme et leur structure est la clé d’un bon ponçage, car plus le frottement est faible, plus la chaleur générée sera faible et donc plus la coupe du minéral sera efficace, moins le matériau brûlera et moins il s’encrassera.
Par conséquent, l’efficacité de la coupe dépendra fortement de la forme et de la structure des minéraux. Pour obtenir des coupes nettes, qui génèrent moins de chaleur, il est nécessaire d’utiliser des minéraux très tranchants. D’autre part, les coupes plus grossières génèrent des frottements et des températures plus élevés, ce qui rend nécessaire l’utilisation de minéraux à structure conglomérée.
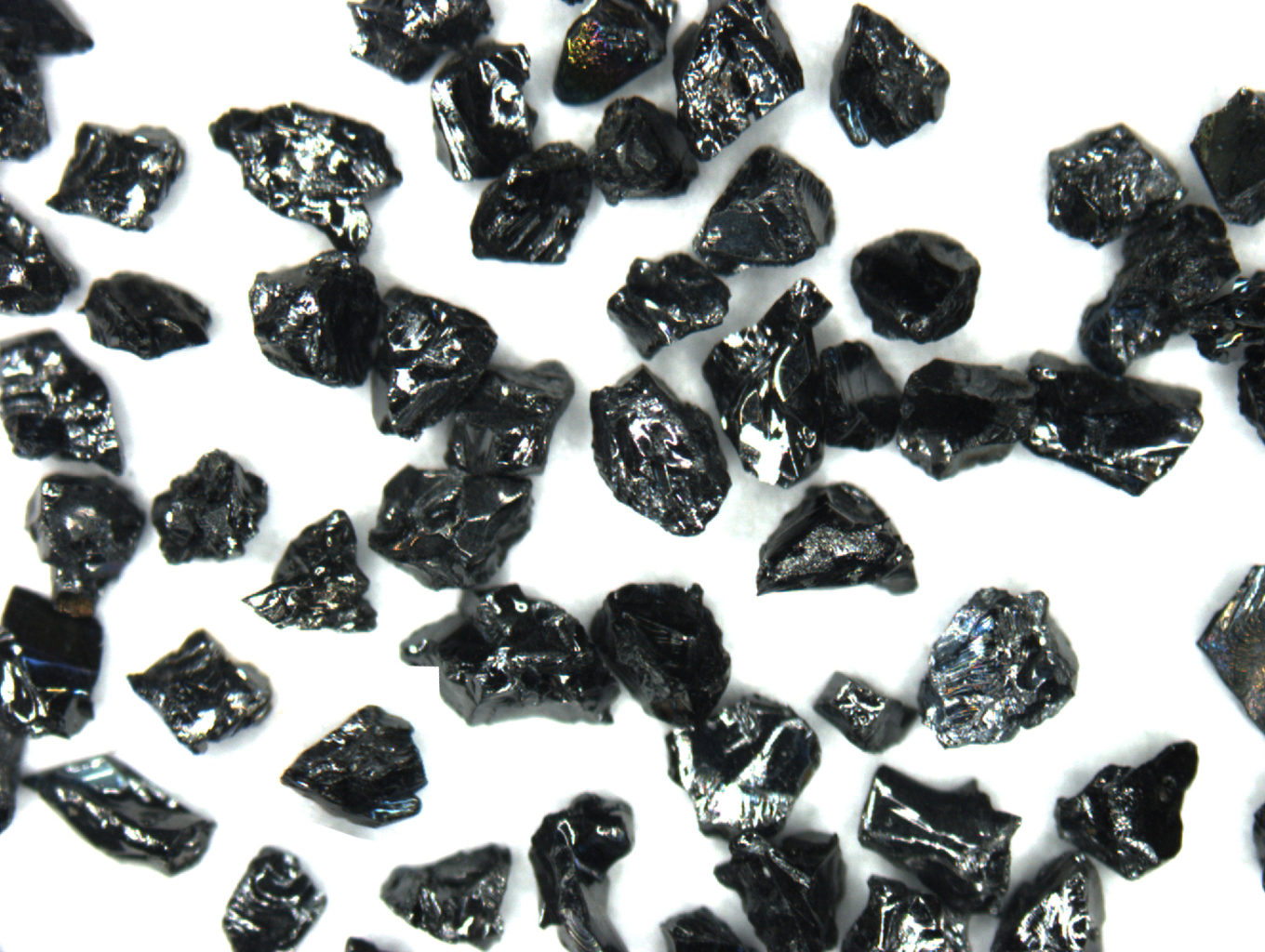
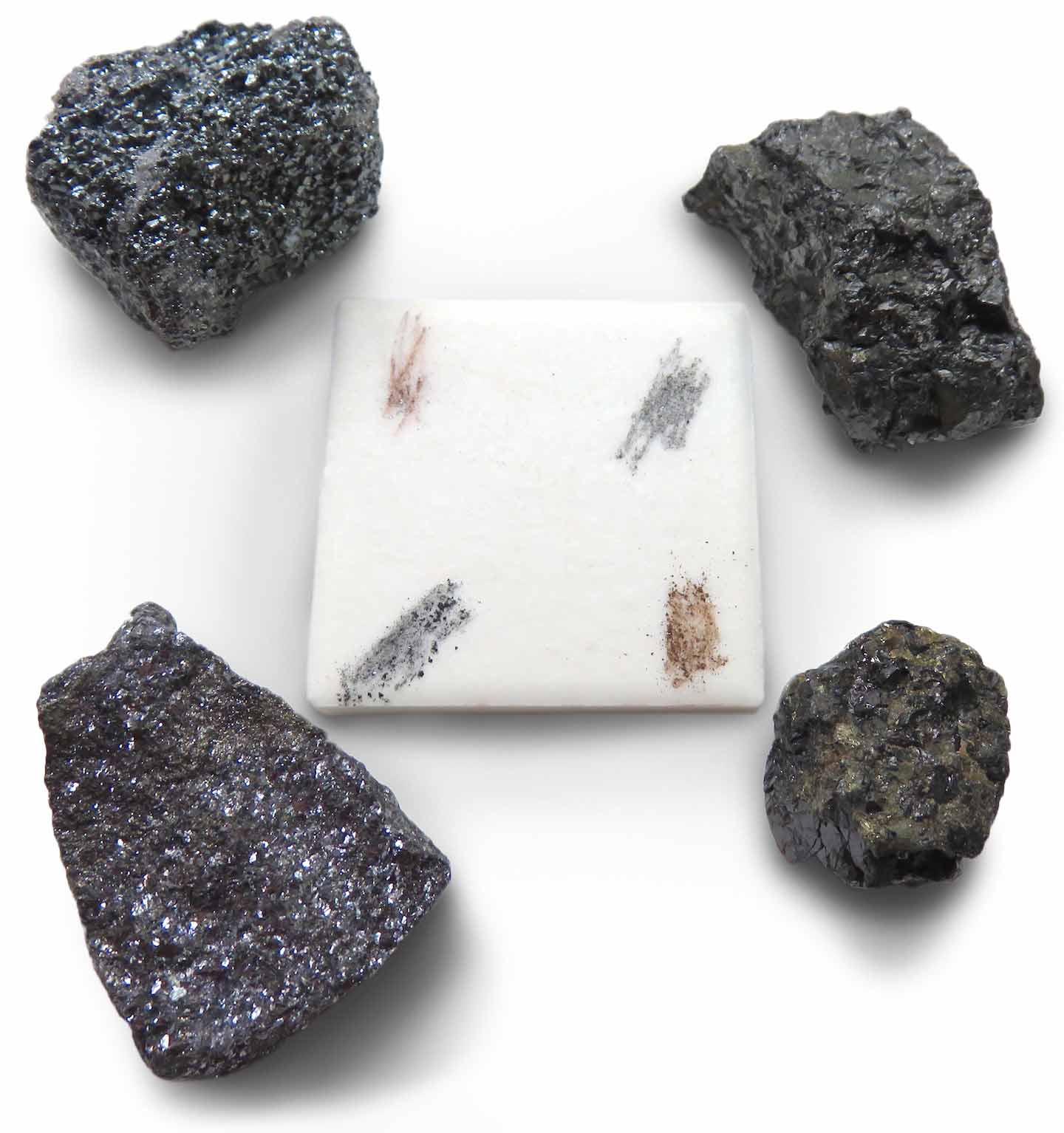
Propriétés mécaniques des minéraux
Outre sa forme et sa structure, chaque minéral possède des propriétés mécaniques distinctes qui lui permettent de résister aux rayures, aux chocs et de s’auto-affûter. Il s’agit de la solidité, de la résistance et de la friabilité des minéraux. Ces trois propriétés sont essentielles pour comprendre le comportement des minéraux dans le traitement des surfaces:
-
Pour poncer une surface (la rayer), on utilise un minéral dont la dureté est supérieure à celle du matériau de la surface.
-
Pour obtenir un pouvoir de démarrage (pouvoir de coupe), nous utiliserons des minéraux capables d’absorber l’énergie générée par ces contraintes et de résister à la rupture.
- Pour maintenir le pouvoir de coupe au fil du temps (auto-affûtage), nous tenons compte des minéraux qui peuvent se fracturer lors des opérations, créant ainsi de nouvelles arêtes plus tranchantes.
Types de minéraux
CR
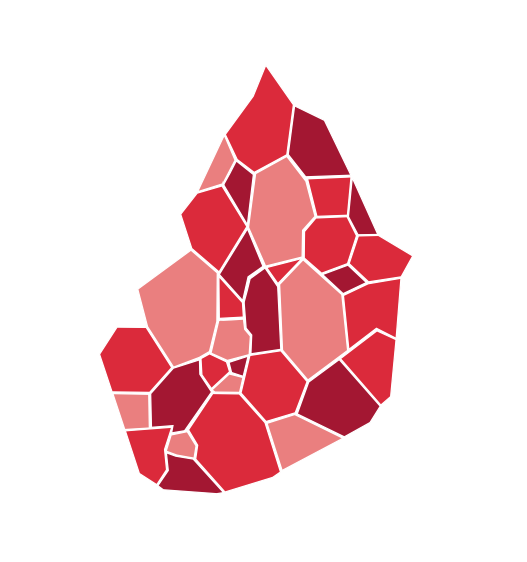
Céramique
TRÈS RÉSISTANT
- C’est un minéral très résistant et robuste.
- Sa structure est microcristalline et ses arêtes sont tranchantes.
- Il est adapté au travail sur le métal et en particulier sur l’acier inoxydable.
- Les meilleurs rendements sont obtenus lors des opérations à haute pression où le minéral se fracture en créant de nouvelles arêtes.
AG
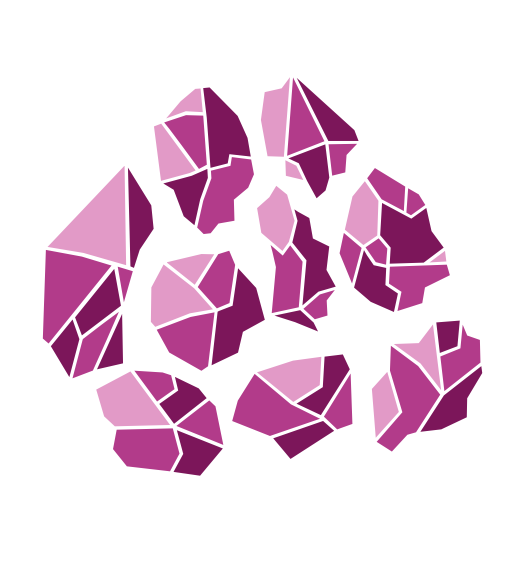
Compact
LONGUE DURÉE
- Il s’agit d’un minéral dur et résistant, de haute performance, avec une finition homogène.
- Sa structure est granulaire, constituée d’un conglomérat de grains de même taille formant un grain plus gros.
- Il se brise sous une pression moyenne, découvrant de nouveaux grains et générant de nouvelles arêtes.
- Il convient au meulage cylindrique de tuyaux, au meulage à lamelles en métal et de bobines.
ZR
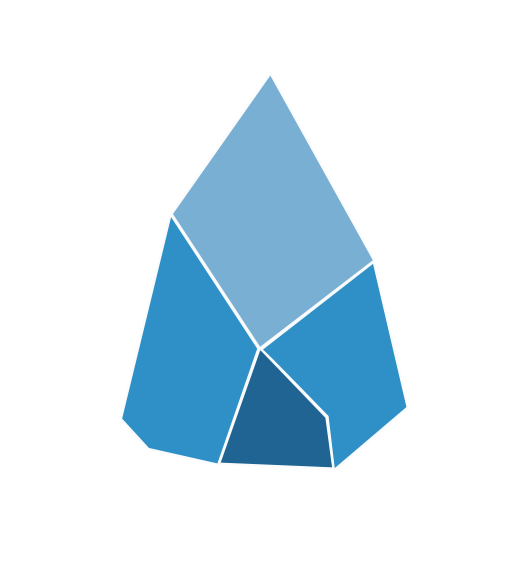
Zirconium
LA CAPACITÉ DE DÉMARRAGE
- Il s’agit d’un minéral dur, doté d’une grande résistance à la rupture et d’une grande capacité de démarrage.
- Il présente une structure cristalline régulière et des arêtes émoussées.
- Il se brise à une pression moyenne générant de nouvelles arêtes.
- Il présente un excellent rapport qualité-prix.
SC
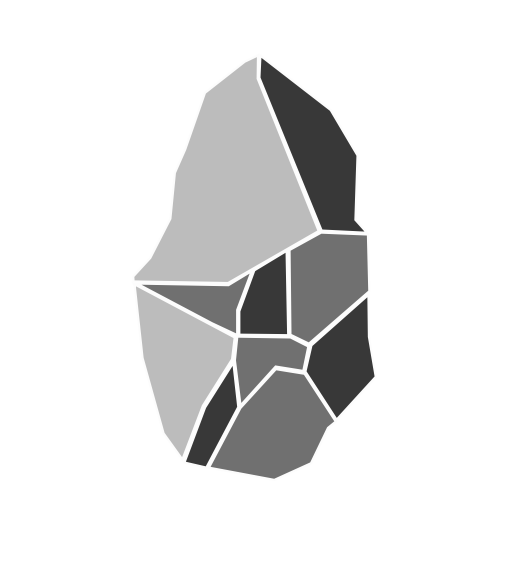
Carbure de silicium
LE PLUS TRANCHANT
- Il s’agit du minéral le plus utilisé pour obtenir les meilleures finitions.
- Sa structure est cristalline et ses arêtes sont très tranchantes.
- Il s’use plus rapidement que l’oxyde d’aluminium, mais comme il est très friable, c’est un minéral robuste.
- Il se casse facilement générant de nouvelles arêtes à basse et moyenne pression.
- Il fonctionne bien sur les matériaux durs, les surfaces rugueuses et lors d’opérations de polissage de surfaces.
AO
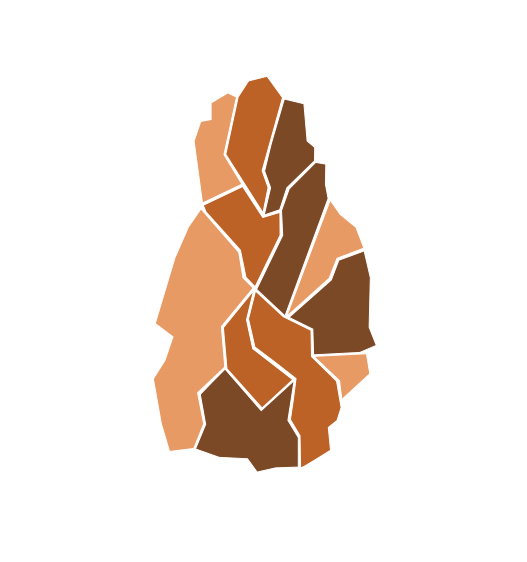
Oxyde d’aluminium
LE PLUS POLYVALENT
- Il s’agit du minéral le plus polyvalent pour tous les matériaux car il présente une combinaison idéale de dureté et de résistance.
- Sa structure cristalline est irrégulière et ses arêtes sont émoussées.
- Lorsqu’il se brise, il ne génère pas de nouvelles arêtes.
- Il en existe trois types : L’oxyde d’aluminium rose et blanc convient aux matériaux souples, tandis que le brun convient aux matériaux plus durs en raison de sa propriété semi-friable.
PIRAMIDAL
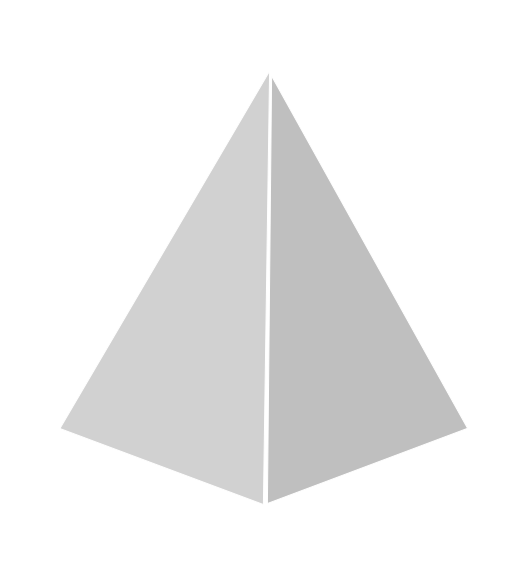
Pyramidal
EXCELLENTE FINITION
- Il s’agit de minéraux mélangés à de la résine de forme pyramidale tous identiques, uniformément micro-reproduits.
- Leur usure est uniforme et continue.
- Il permet d’obtenir d’excellentes finitions et des surfaces homogènes.